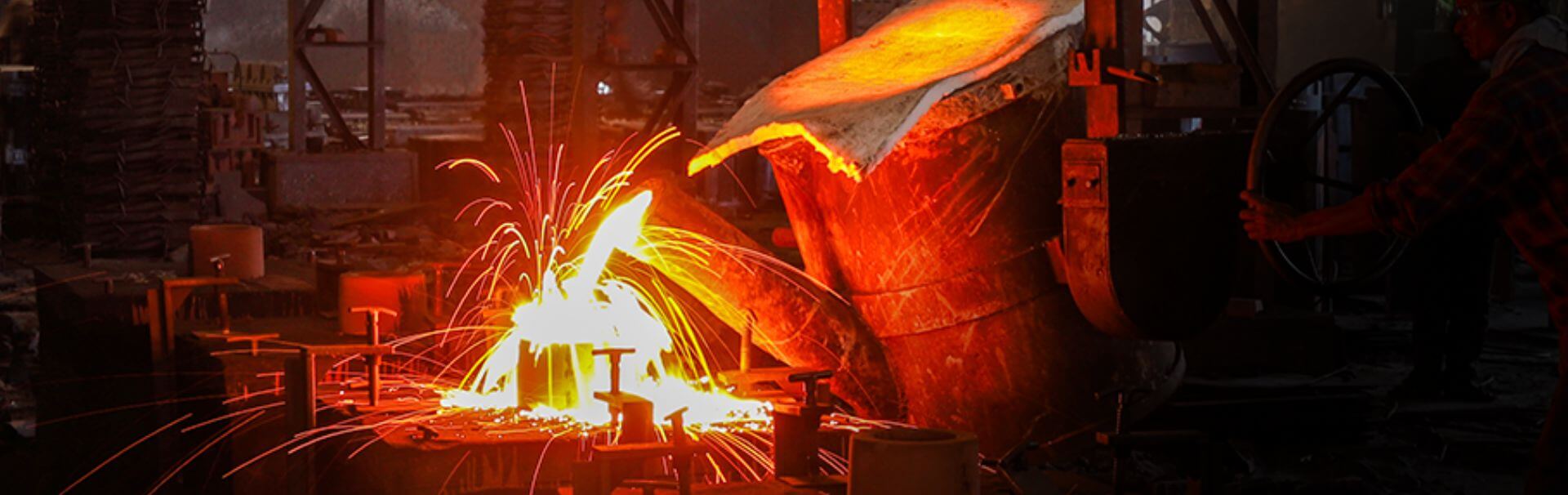
We, as a prominent leader in the industry, have internationally acclaimed standard production facilities with a pure perception to achieve quality excellence and quantitative growth. Using medium frequency induction melting furnaces for optimal metal availability and power efficiency, we keep in mind to ensure everything is perfect. In addition to that, multiple furnaces with modern technology and control systems have been installed from time to time.
It is mandatory for any high-quality casting to begin with a best quality mould. This is always and undoubtedly seen in our investments in technology for producing moulds which result in castings which are best in dimensional accuracy & excellent surface finish.
This moulding Line is one-of-its-kind in India and in addition to that it is a fast Loop moving line. It consists of Automated Track for Pattern Change, Mould Transfer Car, Automated Flow Coater, Gas Fired Oven, and Track for Pouring, Transfer Car for Pouring Loop & Reclamation Plant. We do casting for Frame Size 160 to 315, End- Shield casting, Gearbox casting and Valve Body Casting in this plant.
Size of Each Box (mm) | 1300L x 1100W x 450H |
---|---|
Capacity | 50 moulds per Hour |
Casting Weight | Minimum:80kg |
Maximum:600Kg |
In our Hand-Moulding department we make single piece casting weighing from 30kg to 3000kg for electric motors, end shields, valve component, gear boxes, foundation plates, machine tool casting etc…
Green Sand process consists of 15% of our total capacity. We do casting for Endshields, Alternator parts, Valve Casting, Bearing Housing & Covers in this process. This process is ideal and exceptional for casting with less weight. For many metal applications, green sand processes are the most cost-effective of all metal forming operations. We utilise it as per the necessity of the product specification and client requisites
We have a specially designed ARPA 450 Moulding Line for Green Sand process mould.
Flask Size (mm) | 700 x 700 x 250 |
Bunch Weight | 10-80 Kgs |
Utilising our expertise for making cores of various types, we enable the best equilibrium of economy and perfection in regards to using the perfect type of core for each product with the help of our industry experts.
Shell Moulding Process, Cold Box and Furan no bake process produces new cores in different sizes and shapes.
Fettling is a process of removing excess material from castings often formed by the die’s parting lines during the casting process when molten metal is injected into the mould. For Surface cleaning we use Hanger type and Tumblast type shot blasting machines. We use the latest grinding machines and grinding technology in order to ensure that each and every casting is well finished. These are precisely and carefully executed as the margin of error is really less in this.
Type | Size | Quantity |
---|---|---|
Hanger Type | 1200L x 1800W | 1 |
1000L x 1200W | 3 | |
Tumblast | 900L x 900W | 1 |
Castings can be finished with a range of painted finishes to meet client specifications. Castings are painted using Flow coating, Spray coating or Dipping Process which strictly adhere to C3 & C5 Painting Process. Painted Castings
undergo rigorous paint quality checks which further increases the casting aesthetics.
We have a pattern shop where we maintain our customers patterns. We do not make patterns but if required we arrange for pattern making from some of the best pattern manufacturers in India.